After Covid blues, French saxophone maker hits the right note
MANTES-LA-VILLE
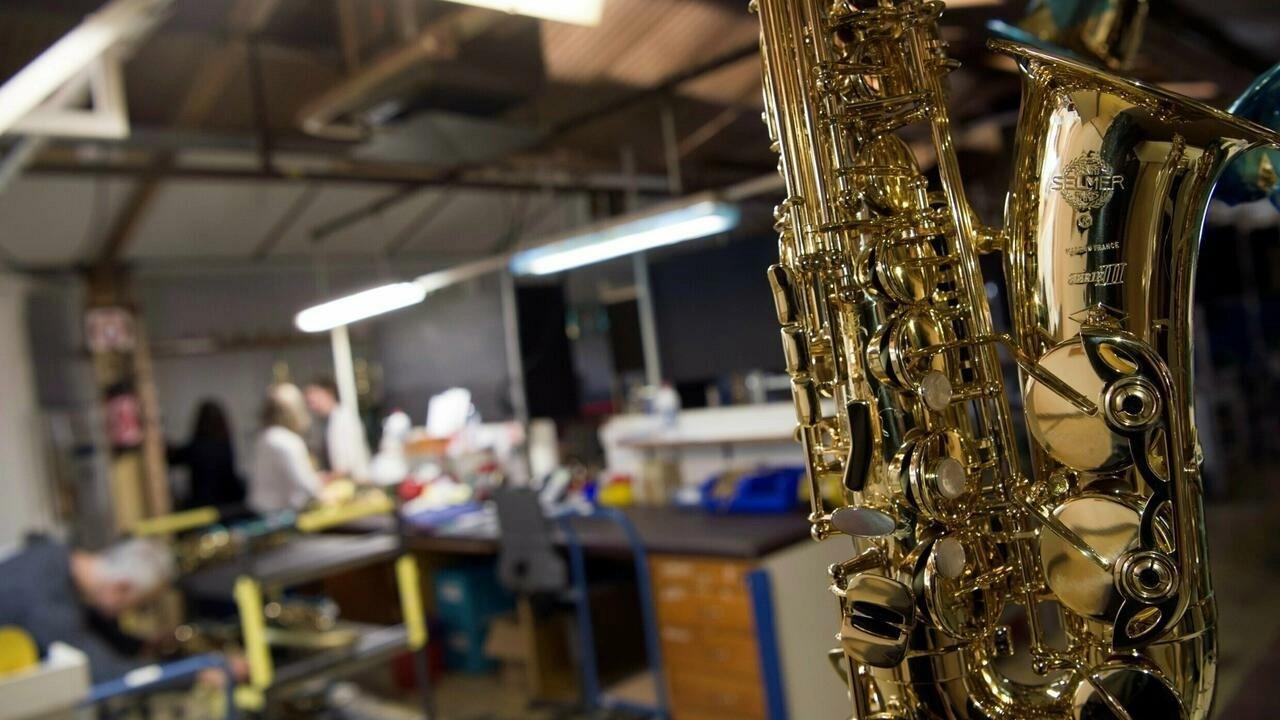
After the financial blues of the COVID-19 pandemic, the French saxophone maker favored by American jazz greats celebrates its 100th birthday looking to expand further in Asia and the United States.
Selmer experienced two difficult years after the pandemic began in 2020, the company’s executive chairman Thierry Oriez tells AFP.
“The COVID crisis affected us together with our customers” because “the world of music stopped,” whether that meant shows or conservatory classes.
But now Oriez looks to the future, with sales brimming once more.
“(I’m) convinced we could do more in the United States.”
Around 90 percent of sales are international, with China accounting for one-fifth of them ahead of Japan, South Korea and the United States. The company did not provide any sales figures.
While order books are full, Selmer, like many other companies, faces recruitment difficulties while COVID-19 continues to pose absenteeism problems.
The company was founded by clarinet player Henri Selmer in 1885 but produced its first saxophone in 1922.
Selmer’s instruments have been played by jazz legends including John Coltrane, Stan Getz and Sonny Rollins.
The family business was sold in 2018 by its heirs to European private equity group Argos Soditec. A delivery subsidiary for Asia was established in 2020.
Oriez took over the business in July from Jerome Selmer, a great-grandson of Henri Selmer.
The instruments are made at a factory in Mantes-La-Ville, just west of Paris. The company also owns a laboratory that works with musicians to develop new models.
Finishing touches and assembly of Selmer’s Axos series, a new collection less expensive than the company’s other instruments, are completed in China. An alto saxophone costs 3,150 euros ($3,430) while a tenor is worth 4,150 euros ($4,500).
Oriez says the new collection “allows us to be more aggressive in the Chinese market”.
While the Mantes-La-Ville factory has motorized precision machinery to craft some of the 700 pieces that make up each instrument, a large part of the work is still carried out by hand.
Artisans cut sheets of brass, use blowtorches to bend them into shape, mount the keys on the tube, polish the instrument and engrave Selmer’s logo on it.
Engraver Morgane Duhamel spots an imperfection and adds by hand “a small engraving that will be personalized and will offer the customer a unique instrument”.
Eric Bruel, who makes the saxophones’ horns by turning the brass tubes on a mandrel, said the search for new tones “has an influence on the treatment of the metal: the reheating temperature with the blowtorch, it will be more or less strong, more or less long.”
“Selmer has always walked the line between modernity regarding tools and the other slightly Amish side: we still do the forging, the welding and polishing by hand,” Bruel said.
“In almost 30 years at the company, I’ve seen many changes in tools, the families of instruments, the musical evolution with young saxophone players who do not necessarily have the same sounds as their elders,” he said.